Our commitment to sustainability
Here at Simmonsigns, we are determined to do our best to preserve the world’s natural resources. Here are some of the actions we are taking to help us achieve our goal.
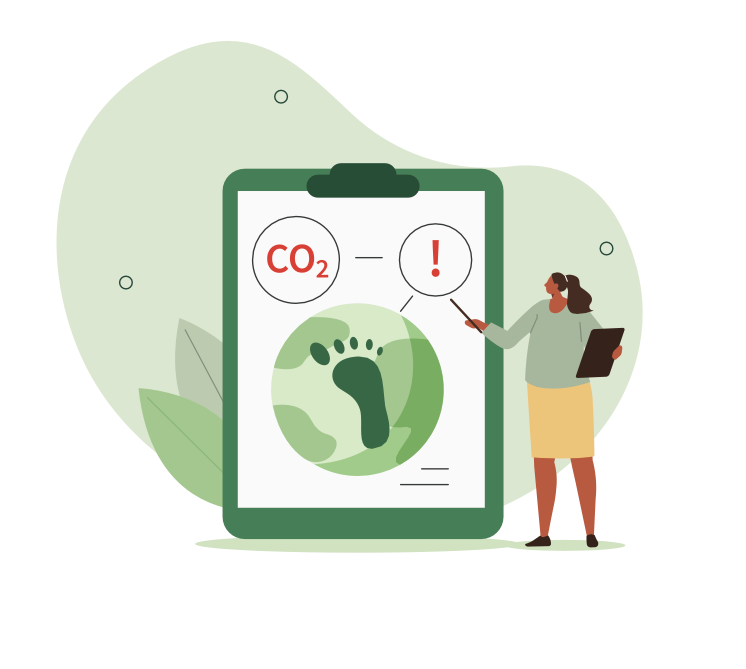
In manufacturing and delivering our products
We are committed to reducing our carbon footprint in the manufacture and assembly of our products. We hold ISO 9001 2015 Cert 602516 and ISO 14001:2015 Certificate No. EMS 553730 which help guide and audit our activities, and reduces waste throughout our processes.
As technology has improved, we have been able to use fewer LEDs, reducing power consumption. One example is the changes we have made to our LUA traffic sign light. Since 2007, the product has moved from 12 LED 20W, to 8 LED 12W, to 3 LED 6W, and right down to 3 LED 5W.
We design and manufacture for longevity and sustainability. For example, the bodies of our LUA and LUB traffic sign lights are made from cast aluminium. We have also made sure that our LED gear trays in the sign lights can be upgraded as technology progresses so that waste is minimised and the sign lights have a long, productive life.
We have also focused on the transport of our products. For example, our traffic safety bollards are covered with a dust sheet and stacked on pallets to optimise density and reduce packaging. LUA sign lights are packed together in fives, in a single box, with minimal cardboard waste.
We use FSC accredited partners for all packaging materials and we optimise our use of these materials. For example, we shrink wrap pallets for bulk bollard orders rather than packaging them individually.
‘Goods In’ materials for manufacture and assembly - such as posts for sign lights - are delivered in reusable stillages with zero waste. Our cast sign light heads arrive on wooden pallets with no other packaging; those pallets are then reused.
We recycle more than 80% of our waste generated through the production process. We also consider the waste stream that we create for our customers and aim to minimise it, particularly while installing our products at the roadside.
We produce products that consume less energy (e.g. our solar-powered road safety products, LED lights).
We reduce waste through our commitment to ISO 14001. Plastic and metal used in the manufacture and assembly of our products can be recycled. This means that many of our finished products, including the plastic bollards, are entirely recyclable.
To reduce carbon emissions, we share transport burdens with a number of our customers.
Within the business itself...
We are planning a review of our overall energy usage to see how we can make our headquarters more energy efficient. This includes reducing both lighting and heating, increasing window insulation etc.
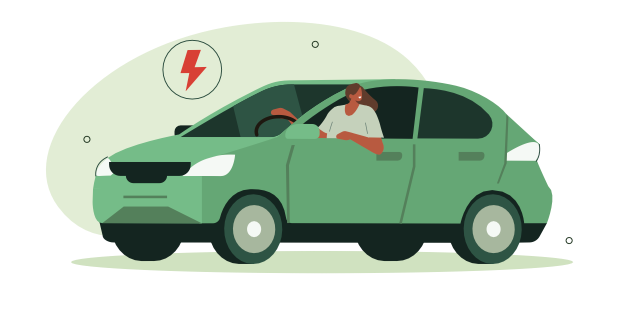
As our business managers change their company vehicles, we are adding hybrid cars to the fleet. Our most recent addition is an all-electric car. We have electric charging points at our headquarters for company vehicles.
Across the business, we recycle as many materials as we can including paper, ink cartridges, aluminium, timber and batteries.
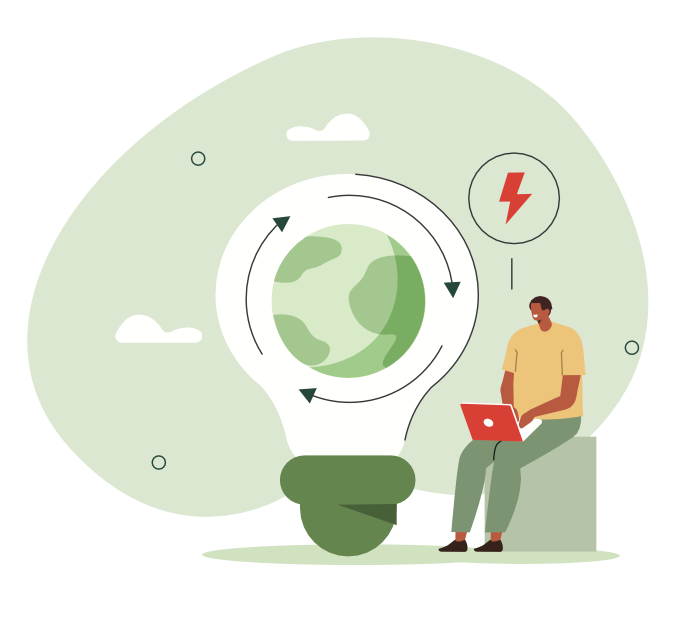
Reducing plastic
We have made changes to our Belisha beacon packaging to reduce single-use plastic waste and ensure it is kept to a minimum. Instead, we now use recyclable packaging.
We use paperless ordering and invoicing, and we accept orders electronically. We can submit our invoices electronically, either by email with PDF attachment, or by entering them onto a web portal.
Reducing paper
As part of our work to reduce our use of paper, we have made huge strides with recycling and only printing documents when absolutely necessary.
A significant milestone for us is the recent introduction of a QR code which signposts customers to all our installation guides in the Resource Centre. Previously, printed instructions were sent with every product. Now we have replaced that with one QR code label on every product. Not only are we saving paper and ink, but there is an increase in production efficiency and a decrease in cost.
Additionally, customers and contractors alike are able to access product data and installation instructions wherever and whenever necessary.
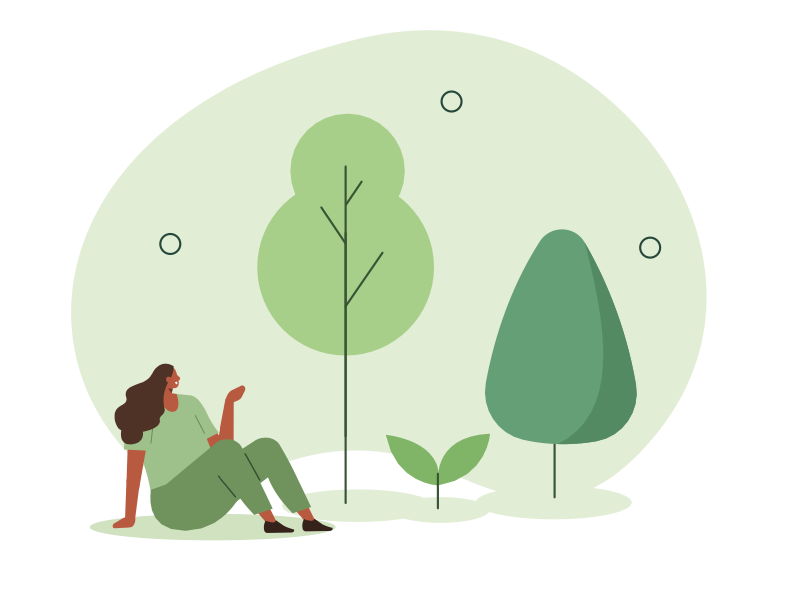